Selecting the right surface drilling rig is crucial for the success of your mining, geotechnical, construction, or blasting projects. Whether you need to drill deep holes or manage challenging geological conditions, the right equipment can significantly boost productivity, safety, and cost-efficiency. In this comprehensive guide, we'll walk you through the key factors you should consider when choosing a drilling rig for your surface project.
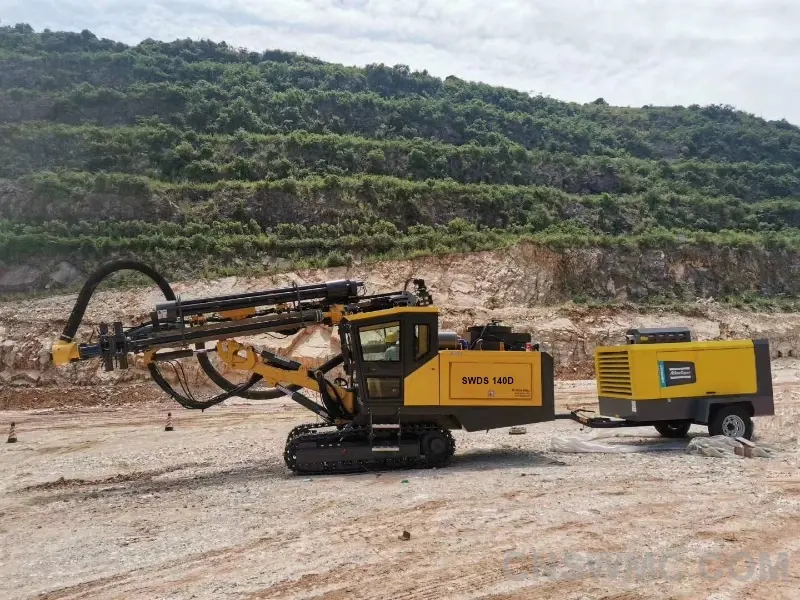
1. Types of Surface Drilling Rigs: Which One Is Right for Your Project?
Different types of surface drilling rigs are designed for specific tasks, and choosing the right one is essential to your project’s success. Here are the most common types:
- Rotary Drilling Rigs: Best for deep drilling and large-diameter holes. Perfect for mining, water well drilling, and geothermal drilling projects.
- Down-the-Hole (DTH) Drilling Rigs: These rigs excel at hard rock drilling, offering high penetration rates and efficiency for mining, geotechnical exploration, and blasting projects.
- Top Hammer Drilling Rigs: Designed for smaller to medium-sized projects in construction and small-scale mining. Known for their percussive action that provides fast drilling.
- Hydraulic Drilling Rigs: Ideal for geotechnical investigations, water well drilling, and mineral exploration, offering versatility and high power for a range of drilling conditions.
Selecting the right rig type depends on your project’s drilling depth, rock types, and hole diameter.
2. Consider the Geology and Ground Conditions
Geological conditions directly impact the performance and efficiency of your drilling rig. Whether you're drilling in hard rock, soft rock, or dealing with overburden, the right rig choice ensures the best performance.
- Hard Rock: For hard rock drilling, DTH or top hammer rigs are ideal due to their high impact force.
- Soft Rock: Rotary drilling rigs are more effective for softer conditions, as they can manage overburden and softer soil layers more efficiently.
- Water Table & Groundwater: If you're drilling near the water table or in areas with groundwater, select a rig designed to handle wet drilling conditions.
Understanding the geology at your drilling site ensures better efficiency and safety.
3. Drilling Depth and Hole Diameter
When determining the right surface drilling rig, consider the drilling depth and hole diameter:
- Shallow Drilling: For shallow holes (less than 100 meters), consider compact rigs that are portable and cost-effective for shorter, quicker projects.
- Deep Drilling: For drilling deep holes, select a high-capacity rotary rig or DTH rig, which are designed for deeper penetration and larger hole diameters.
Always ensure that the rig can handle the required drilling parameters for your project’s specific needs.
4. Rig Mobility: Access to Challenging Locations
Rig mobility is another important factor. Depending on your project site’s terrain, you'll need a rig that can access hard-to-reach or remote locations.
- Remote Areas: If your drilling project is located in difficult-to-reach areas, opt for rigs with high mobility such as crawler tracks or all-terrain wheels.
- Tight Spaces: For urban or construction projects with limited space, compact rigs are ideal for maneuvering within confined areas.
- Fast Setup: In fast-moving projects, choose rigs that offer quick mobilization to reduce downtime.
Having a rig that can easily navigate and set up at the project site ensures maximum efficiency.
5. Power Source and Fuel Efficiency
Fuel consumption and power sources can significantly affect the long-term costs of your drilling project. Here are the main power sources for drilling rigs:
- Diesel-Powered Drilling Rigs: Widely used for heavy-duty tasks, diesel rigs offer high power for mining and geothermal drilling projects.
- Electric Drilling Rigs: Electric rigs are more environmentally friendly and ideal for urban projects or areas with reliable power grids.
- Hybrid Drilling Rigs: Combining diesel and electric power, hybrid rigs provide flexibility and improve fuel efficiency, making them suitable for a range of drilling conditions.
Selecting a rig with the right power source for your project will help you manage both costs and environmental impact.
6. Durability and Maintenance Considerations
Drilling operations, especially in harsh conditions, demand equipment that is durable and easy to maintain. Choose a drilling rig that is:
- Built to Last: Rigs made from high-quality materials are designed to endure tough conditions and minimize downtime.
- Maintenance-Friendly: Look for rigs with accessible components for easier servicing and routine maintenance.
- Spare Parts: Ensure that spare parts are easily accessible, and that the manufacturer provides reliable after-sales service to keep your rig operational.
Proper maintenance is crucial to extending the life of your rig and reducing long-term costs.
7. Safety Features in Drilling Rigs
Safety is paramount in any drilling operation. Look for rigs with these essential safety features:
- Automatic Shut-Off Systems: These systems immediately stop drilling if a malfunction occurs, reducing the risk of accidents.
- Rollover Protection (ROPS): Protects operators in case of rig tipping or accidents.
- Operator Safety Monitoring: Real-time monitoring of drilling conditions helps ensure safe operation under high-pressure conditions.
Make sure that the rig meets all relevant safety standards to protect workers and operators.
8. Cost of Ownership: Balancing Upfront and Long-Term Costs
The total cost of ownership of your drilling rig should include both the initial purchase price and the ongoing operational costs:
- Upfront Costs: The initial price can vary depending on the type of rig and its features. Ensure that the rig fits your budget while meeting your project’s requirements.
- Operational Costs: Consider fuel consumption, maintenance needs, and spare parts availability when evaluating the total cost of ownership.
- ROI Considerations: A more expensive rig might offer higher performance and better long-term ROI through increased productivity and lower operational costs.
By carefully evaluating the total cost, you can choose a rig that provides the best value for your drilling project.
Choosing the Right Surface Drilling Rig for Your Needs
Selecting the best surface drilling rig for your project is crucial for ensuring efficiency, safety, and cost-effectiveness. By carefully evaluating factors like drilling type, geological conditions, rig mobility, power source, and maintenance needs, you can choose the rig that aligns with your project’s goals.
Ready to start your drilling project? Make sure you select a rig that matches your specific drilling requirements, and don’t forget to consult with experts to ensure optimal performance.